Safety and Security Redefined with Carbon Fiber Technology
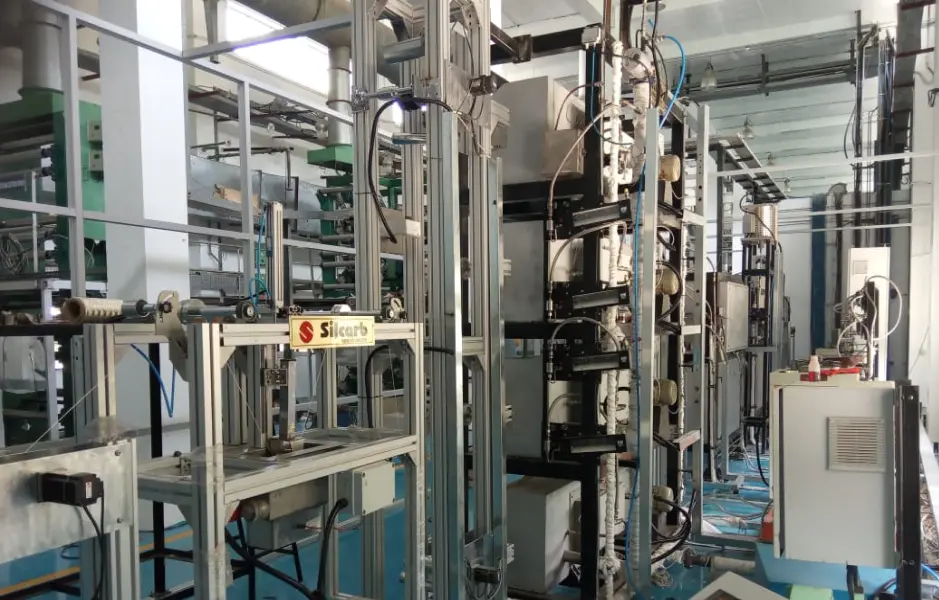
The unwavering commitment to constantly work on innovation, and Silcarb’s expertise in high-temperature and processes under the guidance of material science, make us ready and well-equipped to cater to the constant demand for Carbon fiber equipment manufacturers in India and their solutions across diverse industries.
Our nation’s progress towards self-reliant strategies in the material sector took us to be the undisputed leader with the successful installation of the country’s first-ever carbon fibre equipment manufactures in India with the first-of-its-kind production line. This groundbreaking achievement has paved the way for opening our doors towards technological advancements in diverse industrial sectors.
The Importance of Carbon Fibre for India
How can Silcarb assist in these sectors with our quality products and expertise
Carbon fiber, also known as graphite, is a reformatory material well-known for its exceptional combination of great tensile strength of the carbon fibers, with its lightness, and extreme heat tolerance at the same time. These properties make the carbon fiber material properties ideal for various applications across diverse industries such as:
- In Aerospace, carbon fiber usage in aircraft components minimizes aircraft load wherever possible, leading to improved fuel efficiency and enhancing payload capacity.
- In Defense, carbon fiber provides superior ballistic screening for military vehicles and defense equipment.
- In the automobile sector, the use of carbon fibre in car body parts manufacturing gives way for lighter, more efficient vehicles with upgraded performance.
- In Sports & Recreation, carbon fiber is used in various sporting equipment like cycles, gymnastic bars, rackets, poles and others for superior strength-to-weight ratios, increasing performance and user experience.
Who are India’s first carbon fiber equipment production line – It is Silcarb
Silcarb leads the way forward
With Indian National Aeronautics, Silcarb is triumphant in installing India’s first carbon fiber, carbon fiber equipment production line, setting a benchmark milestone in the advancing high-capacity ovens, furnaces and fibers.
Silcarb is an expert in Carbon Fibre Cycle Production:
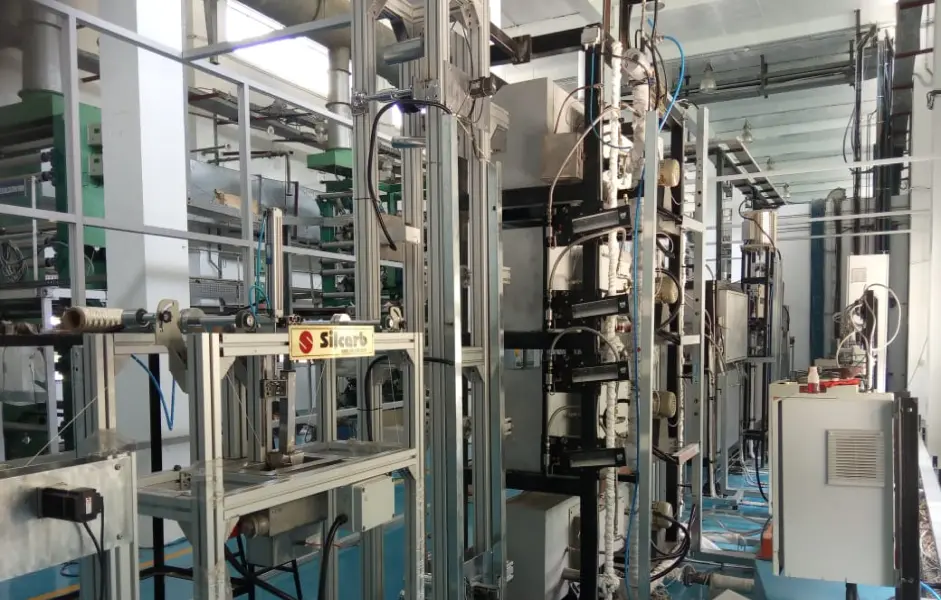
- Silcarbs Soaring High in the Realm of Aerospace:
The vast expansive world of aeronautics thrives on creativity and innovation, constantly pushing the boundaries of resilience, lightweight, and heat-resistant products. In this pursuit, leading names of carbon fibre equipment manufacturers in India like Silcarb are playing a game-changing role, offering a multitude of opportunities for new-age aircraft design and manufacturing.
One of the most striking implementations of Silcarb’s carbon fibre in aerospace engineering is the concept of load reduction. As the conventional metallic components can weigh on the heavier side, it significantly increases an aircraft’s fuel consumption and parallelly decreases the efficiency and payload capacity. By replacing the aircraft equipment with carbon fibre equipment wherever possible, such as wings and the main body housing the pilot and passengers area of an aircraft, our carbon fibre material properties invented by our engineering scientists, comes truly as a breakthrough achievement at Silcarb.
The exceptional heat tolerance capacity of Silcarb’s carbon fibre sheets is another crucial aspect of aeronautics. Modern jets generate immense heat in the engines, and certain aircraft components have the capabilities to withstand extreme heat conditions. Silcarb’s carbon fibre composites are the undisputed leader among the carbon firbre equipment manufacturers in India, offering classy thermal stability compared to conventional old concepts and materials.
Furthermore, Silcarb’s carbon fibre composites boast excellent strength bearing capacity, a crucial feature for aircraft that endure continued stress cycles during the flights. These composites can take repeated loading and unloading without falling prey to fatigue cracks, ensuring a durable lifespan. Silcarb’s carbon fibre composites promise unimaginable strength-to-weight ratios, enabling designer engineers to create lighter, more aerodynamic friendly aircraft.
By the adaptation of Silcarb’s carbon fibre in India’s aeronautics industry, India reduces its dependency on imports, strengthening self-sufficient conditions in our country, especially in a sector vital for national security and economic growth always.
- Fortifying the Indian Defense Mechanism with Silcarb’s Carbon Fibres
The expansive realm of Indian defense is evolving at a fast pace, and unmanned systems (UxS) have cropped up with great popularity among the forces and are playing an increasingly crucial part, given the increase in threat from various factors. Carbon Fibre Equipment Manufacturers in India, like Silcarb, are a leading provider of vital components of the machineries to keep up with the capabilities of next-generation defense technologies. Silcarb’s high-performance carbon fibre usage predominantly offers several advantages for UxS design and upgradation.
Apart from the weight reduction, Silcarb’s carbon fibre composites also fare best in electromagnetic shielding, a critical aspect for the unmanned systems such as drones or choppers operating in hostile environments. These composites can resist electromagnetic signals, elevating stealth mode of the unmanned systems and reducing their visibility that threatens detection by enemy radars.
In addition, the durability of Silcarb’s carbon fibre usage is essential for the unmanned systems to survive hostile conditions, uncompromising the impact resistance, and be battlefield ready, ultimately strengthening its national security posture.
- Strengthening Structures All the Way with Silcarbs Carbon Fibre
Dilapidated building structures and those damaged by natural calamities such as earthquakes or floods pose a significant risk to safety and security. Here is where Silcarb’s Carbon Fibres come to the rescue.
Silcarb, being the top carbon fibre equipment Manufacturer in India, their products are made to excel in strength-to-weight combination. This allows the carbon fibre material applications to work best in reinforcing these layers to beams, ceilings, columns, and walls without bringing the whole structure down. This non-intrusive way enhances and extends their lifespan further, and to withstand seismic loads and avert disasters.
With the latest advancement in technology, carbon fibre from Silcarb is lightweight, and easy to handle minimizing additional stress on the existing structure. However, when compared to conventional metal reinforcements, carbon fibre proves to be of higher strength and durability, giving building owners a new lease of life into renovating deteriorating structures and ensuring the safety of occupants.
Are you Looking to exploring with the Carbon Fibre Equipment Manufacturers in India?
At Silcarb, it is our expertise and your selection
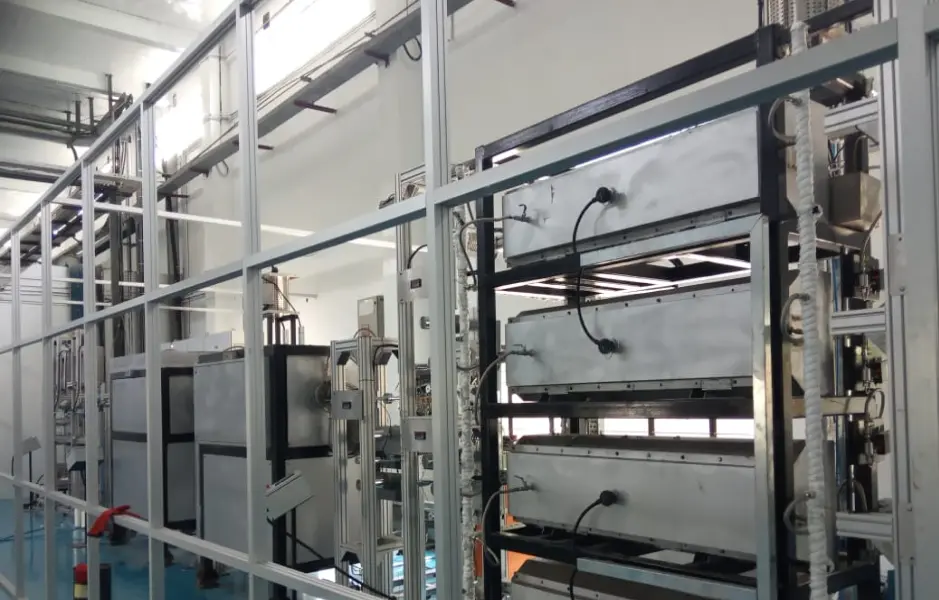
Our expert team always emphasizes the relationship with our clients to be more valuable as there is a long journey that has begun with the association of mere buying and selling scenario. We expedite the process from selection, implementation and servicing regularly, and that is what makes us the leader in carbon fibre usage techniques. We stand by your since-
- At the initial step, Silcarb’s team of experts assist you in selecting the most appropriate Carbon Fibre grade and type based on your specific application requirements. Different fibre types offer variations in strength, stiffness, and other properties to suit diverse needs.
- The fabrication by Silcarb can be custom-made using carbon fibres in the components to design specific sturdy frames and structures. This ensures optimal withstanding capacity to safeguard your equipment.
- Support and Assistance by Silcarb comes with comprehensive technical servicing throughout the entire journey, right from material selection to component integration at the final stages, and beyond. Our team is dedicated to answering your queries and guiding from implementation to the running stage.
What is the The Future for Carbon Fibre Equipment in India, with Silcarb
The milestone achievement of setting up of India’s first Carbon Fibre production line by Silcarb marks an eventful benchmark for other manufacturers and technological organizations in the nation. With domestic production scaling up steadily, Carbon fibre is expected to become a commodity of exchange with other countries, making it a revenue-generating factor for the country and industrialists alike. There is scope for becoming more accessible and cost-effective, further accelerating carbon fibre usage across various industries.
Silcarb: Leading the Way as carbon Fiber Equipment Manufacturer in India
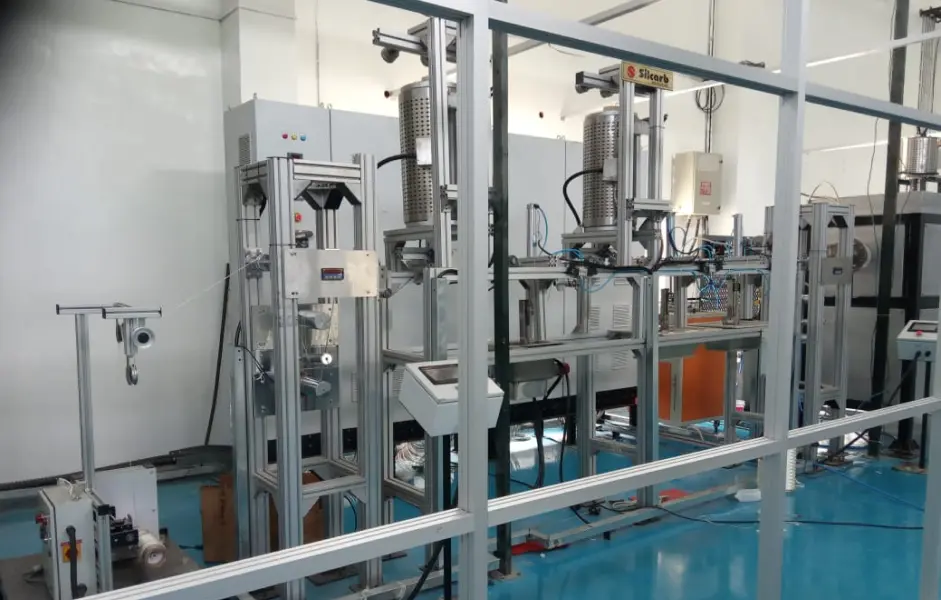
Silcarb’s drive towards innovation and its focus is to play a pioneering role in establishing a domestic carbon fibre production line in the company paves the way not only for individual sector growth but also the growth of the nation. With its unmatched domain knowledge and expertise in high-temperature manufacturing and treating processes keeping material science as the base, Silcarb, the leading carbon fibre manufacturer in India is well-equipped to cater to its growing demand across various industries.
With its recent success in being the first production line of Carbon Fibre for Indian National Aeronautics wing, the future potential collaborations with other prestigious institutions will pave the way for harnessing the power of Carbon Fibre material properties in other industries alike
Carbon Fiber Heat Treatment
Heat treatment is a crucial process in the production and enhancement of carbon fibre materials. This treatment involves exposing carbon fibres to high temperatures in an inert atmosphere, which serves several purposes:
Stabilization:
First, the precursor fibres, such as polyacrylonitrile (PAN) or pitch, undergo the process of stabilization. This involves heating the fibres up to temperatures as high as 200-300°C in an oxidizing environment. During this phase, the fibres undergo chemical changes that make them infusible and prepare them for the next stage.
Carbonization:
After stabilization, the fibres are once again heated to temperatures ranging from 1000°C to 1500°C in an inert atmosphere, typically prominent in nitrogen. This process frees the material from non-carbon elements like hydrogen, oxygen, and nitrogen, resulting in a material that is composed of more than 90% carbon. We can say that carbonization is the crucial stage in the carbon cycle that enhances the strength and rigidity of the fibres.
Graphitization:
Certain applications require an even higher strength and thermal conductivity. To achieve this, the carbonized fibres are further heated to extremely high temperatures between 2500°C to 3000°C. This stage transforms the carbon structure into a more graphitic form, aligning the carbon atoms into a crystalline structure. Graphitization, therefore, increases the stiffness and electrical conductivity of the fibres.
Post-Treatment Processes:
After the primary heat treatments, carbon fibres have to undergo additional processes such as surface treatment and sizing, depending on the application of the fibres. Surface treatment improves the bonding between the fibres and the matrix material in composite applications. Sizing the a process that involves applying a protective coating to enhance the handling and the compatibility with resins.
Benefits of Heat Treatment
Enhanced Mechanical Properties:
Heat-treated carbon fibres exhibit superior tensile strength and higher modulus of elasticity, making them ideal for high-performance applications such as aerospace, automotive, and sports equipment.
Thermal Stability:
The heat treatment processes result in drastically increased thermal stability of carbon fibres, enabling them to withstand high temperatures without significant degradation.
Electrical Conductivity:
Through graphitization, carbon fibres gain remarkable electrical conductivity, which is crucial for their applications in electronics and electromagnetic shielding.